rotection test's - A relic of old times?
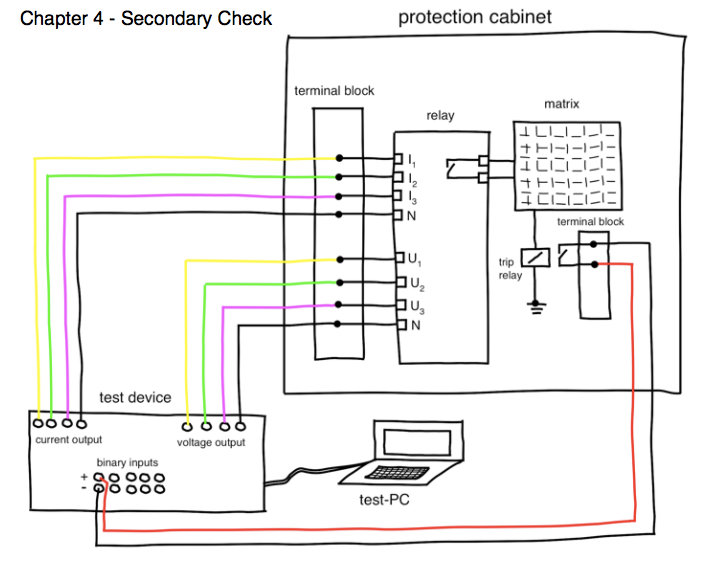
Our protection and control systems are becoming increasingly more and more complex. To be exact, we are dealing with system systems. On closer inspection, the simplest protective devices, each individually, are their own systems, which have several control interfaces, measurement, protection and control monitoring and recording functions. These IED's then operate in interconnection, e.g. communication-based busbar protection or other scenarios, which in turn have to be combined with neighboring protection systems (distribution network protection / transmission network protection / power plant protection) into a larger system.
In this "wild mix" of protection and control systems, we now have an almost completely self-monitoring digital IED generation. Modern devices achieve very high availability since both software and hardware are "self-monitored" and device and / or system faults are immediately displayed. The high availability of the smallest units, our IEDs, is a key factor in achieving optimum availability for all higher-level systems and the entire electro-energy system. In the era of multi-optimized digital device generations, the following question must be allowed:
Are protection test's still up-to-date?
To answer this question, it is first necessary to define clear vocabulary. Only if we use the same terms for one and the same content, we are able to communicate fruitfully with each other and to get to the point, so let's go:
Protection tests can generally be divided into the following three test objectives:
1. commissioning test's:
The commissioning test serves to provide complete proof of all functional details of the overall protection system. The test consists of many individual test steps and is carried out within the framework of a plant installation or renewal.
2. repeated test's:
This test is also referred to as "recurring test" and "cyclic test" or "maintenance test". It stands for the test steps, which are carried out at regular intervals, which are regarded as necessary in the context of maintenance.
3. nonstandard test's:
The nonstandard test is an unscheduled test which is used in the following cases:
- after disturbances affecting the function of IED's,
- after a protection system has shown malfunction
- after performing software updates or parameter or configuration changes
- after changes in the system affecting the protection system (eg: renewal of transformer wiring)
This nonstandard test also consists of a composition of individual test steps. In this context, the test step is understood to mean individual tests, such as, for example, measuring of the connected burden within the scope of the transformer test.
Ok but back to the question, do we need protection test's?
For the commissioning test our question can be answered as follows:
Yes! Protection tests are very "up to date". Everything has to be checked! Modern self-monitoring system components must also be tested for function. There is no way around this test, it is obligatory, and nobody will dare to question it seriously.
We are also likely to agree on nonstandard test's. An protections system which has become conspicuous by malfunction, must always be "thoroughly tested". In each case, it is necessary to differentiate between the individual test steps that are actually required. This test is obligatory.
These two protective tests, the commissioning test and the special test, make up the smallest part of all protective tests. The commissioning test is normally carried out only once at the beginning of the life cycle of a protection system. Special tests are always used only if there are hardware or software changes affecting the protection system, or if system malfunctions or malfunctions occur. The most frequent examination of all protection tests, on the other hand, is the repeated test. Here it is worth to look more closely.
The repetition test consists either of a functional test or of a main test which has traditionally been carried out alternately. Here, too, there are regional vocabularies, depending on the system level. What is meant is always the same:
The functional test describes the check of the tripping capability of the protection system, as well as the verification of all binary input and output circuits. Furthermore and all analog inputs are tested (currents and voltages) by checking the operating measurement values on the displays of the devices. In addition, the readout and evaluation of the alarm and fault value memory and the comparison of all actual values with the desired parameters are performed.
The main test consists of a functional test which is additionally extended by a secondary test. In contrast to the pure function test, the response and decay values of the algorithms are also approached and the tolerances of the relay pick up values are detected.
The secondary test is a very essential part of a repeat test. For example, The characteristics of differential protection functions and their harmonics are fully approached and tested. Distance protection functions are usually "bombed" for all types of faults that can be used in operation and for all active zones with dozens of trip and non-tripping points. Thermal characteristics in machine protection also lead to correspondingly high waiting times during the secondary test due to high trip time delays (correct testing is carried out without "down parameterization" the time elements for test purposes ". The test set-up for secondary protection tests alone is time-consuming, since the analog secondary signals have to be simulated and, consequently, also temporarily wired. Tripping and signaling circuits must be connected to the test device so that the test device can measure times and can control the test routine.
And now my humble question: Why the whole thing?
Is it actually necessary, in the context of repeated test's, to carry out the secondary protection test as a fixed component again and again?
I say no. Here an urgent rethought is appropriate. In my working life, I wasted countless hours of running secondary protection tests and "penetrating" the characteristics and response values. Just to end up getting the same result:
Response values and characteristics of modern digital protection devices do not change and:
It's boring. It's so boring doing the same again and again.
I have never encountered an unacceptable pick-up value or an out-of-tolerance characteristic when testing a modern digital protection device. How should this be done if the algorithms of these functions are calculated numeric based on digital technology?
Was that always the case?
No! And that is precisely the reason for our present approach in the conduct of repeat tests. It's in the history of protective engineering and in our sluggish adaptability. Old habits die hard.
1st generation:
The first protective devices were electromechanical. These miracles of mechanical precision had to be maintained at regular intervals and readjusted. Above all, thermal characteristics, which were realized using bi-metal elements, had to be regularly overtaken. Timing elements and tripping zones of electromechanical distance protection devices also required corresponding "amounts of petting". Self-monitoring was not to be considered here. Thorough verification of pick up values and characteristic curves was indispensable here.
2nd generation:
In the second generation of protection technology, operational amplifiers were used for the first time. This revolutionary step towards analogue-static protection also had a major weakness. Due to their age, electrolytic capacitors caused the famous "characteristic drift". We have still re-soldered capacitors, e.g. to restore the underexcitation characteristic curve of a 500 MW generator after it had been "died" in the sub-excited area. The eminently accurate checking of all characteristics, all starting and picking values as well as the tolerances guaranteed by the manufacturer were an important part of every repeat test.
And today?
We still do it like that! Although two things have changed fundamentally. The system-integrated self-monitoring of our IEDs and the digital calculation of our characteristics and pick-up-values have been introduced. We should take this technical quantum leap into account. Cyclical secondary protection tests in the course of re-examination are part of history. Starting with a professional and correct commissioning test, followed by a subsequent warranty test (1st year after initial commissioning test) and running cyclic function tests, we can say: Good bye cyclic secondary test!
The so called main tests can be replaced by simple functional tests.
The previous test cycles must be kept! Some operators are falsely arguing that the high availability of their systems can justify increased test cycles. Our practical experience shows exact the opposite. The cyclic verification of the systems leads to today's high availability. Within the scope of our functional tests, we have repeatedly revealed weaknesses which would have led to elementary protection failures. Relays, release coils and hard-wired sections are still an integral part of our systems despite IEC 61850 and GOOSE and must be tested regularly in the usual test cycles.
In summary, we conclude:
Repeated tests are the most frequently performed protective tests. They are in charge of the largest maintenance costs, which are approximately 2 to 5 times of all commissioning and nonstandard test costs (it depends of course e.g. of test cycles and the kind of protection system). Above all, the secondary protection test integrated therein is responsible. The scope, the duration and the costs of the repeat test can be substantially reduced if we carry out secondary testing in the future only during commissioning and special tests. The check of characteristic curves, as well as starting and picking values, in the course of repeat tests, must be referred to as "water under the bridge" in the age of digital protection technology. Characteristic and parameter drift of the first and second generation of protective devices are a thing of the past.
The usual test cycles of the operators should be maintained, as the weakest members of our protection systems have not completely changed into the present time.
Greetings Alexander Muth
PS: The picture of this article comes from my book "The Bible of the Generator Protection Engineering - The Commissioning Manuel for professionals" in which you will learn the practical implementation of all relevant generator protection tests. In addition, the general way of testing current and voltage transformers is described in detail and is also very useful for non-generator protection issues. With this cooking recipe you have everything under control.
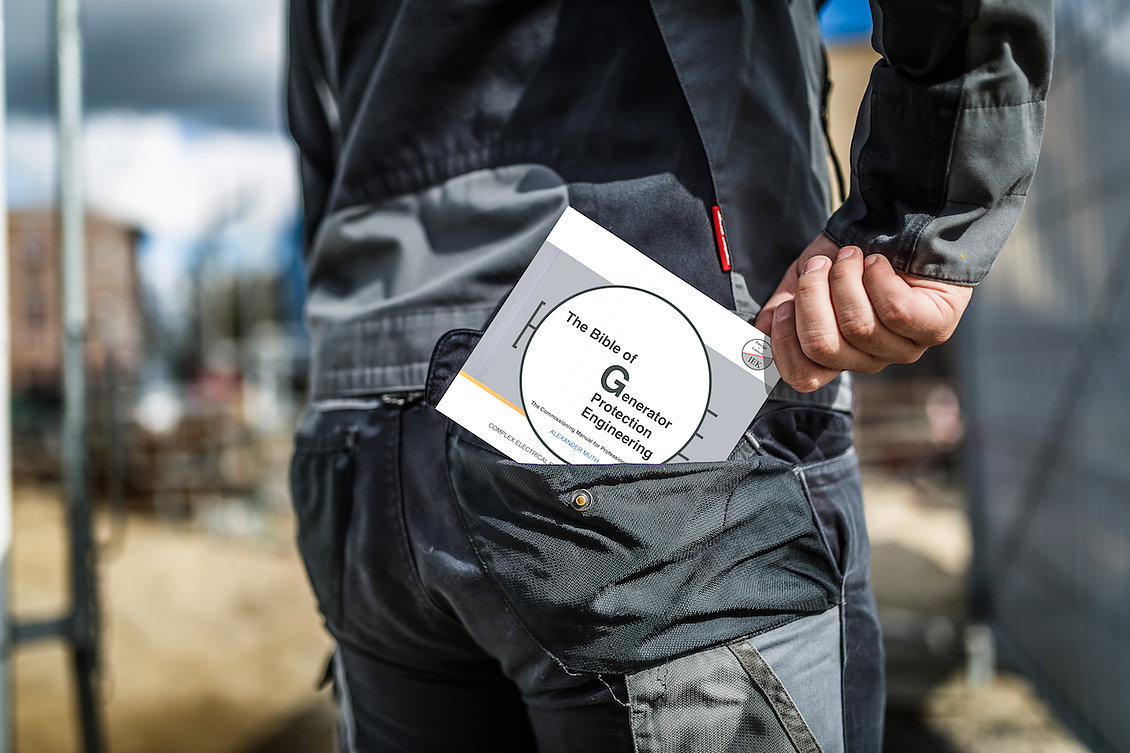